Logistics management is a very important aspect of any business. It helps to bring all of the various departments and operations together to create a well-coordinated supply chain. This supply chain assists suppliers, manufacturers, distributors, customers, and other company stakeholders grow their respective businesses.
Because of its importance, companies must work to ensure that they are practicing the best standards. Several logistical processes and management strategies have a major impact on a company’s overall performance. When followed, it creates a company that functions similar to a well-oiled machine. However, when these processes and strategies go unnoticed, they could also backfire and deal potential harm to the company.
Poor logistics management has the potential to negatively affect most aspects of your business and If you’re not careful, it can undermine your company’s finances, customer service reputation, and brand image.
We’re here to help you identify those 5 poor practices so that you can think ahead and create concrete solutions to address future problems.
4 Poor Practices That Can Negatively Affect Your Company
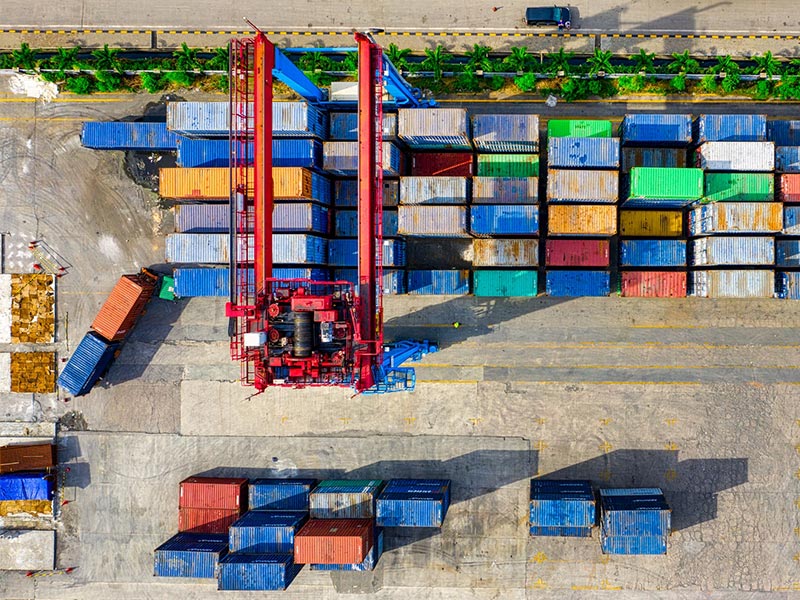
These are the results of how poor practices and management will affect your business in the logistics company.
Poor to Non-existent Customer Satisfaction
When running a business, the mission should always be towards making people’s lives easier than it was before. Products and services should revolve around what the customer wants & needs for them to have a comfortable life. In Logistics, customer satisfaction has been given more emphasis & importance. A customer will keep coming back if you can deliver their products and respond to their queries as quickly and consistently as possible. Make sure that each of your channels has a 24/7 Customer Support service so that you can respond and give your customers the best service they can get. Fulfilling their queries and questions will greatly impact how they will trust your company to handle their future concerns, and quite possibly, make them avail of your services.
Inefficient & Slow Production Time
Consistency and a smooth production process is the key in a successful logistics & supply chain company. If a company can produce deliverables and products, the customer will be satisfied and will go for seconds in coming back to your company for their needs. Make sure that each member of your team knows their roles; proper documentation, create systems and process flows to ensure that each step is completed efficiently, and double-check everything before it goes out. Ensure that your operations are also aligned and designed appropriately so that you can eliminate unnecessary time-wasting activities that can slow down your production line and shipments.
Transportation Bottlenecks
When transportation is not properly tracked or documented, it may cost some time delays and keep item production in a backlog. There will always be the chance that your items may get damaged which will ruin their value and quality. To prevent this, proper planning of routes can be done to prevent longer and costly alternate routes. Make sure that your items are packaged nicely and be able to minimize the space occupied, so that more items can be included in the shipment, leading to less and unnecessary costs in delivering items.
Unable to Invest In Proper Technologies
In our technology-driven generation, businesses that aren’t able to adapt will eventually experience getting left behind by their competitors, leading to a weaker brand presence, which will result in lower sales and conversions to grow the business. There are a lot of tools and technologies that can help you, on the web, with specific parts of your business. Most of them can help you track each shipment and item in your freighter, reduce manual labor needed, and increase security and integrity on your current systems. These technological tools and software bring more precision and accuracy in successfully operating your logistics and supply chain. Other benefits can be gathered from technology, as long as you invest in the right one for your operations. It’s a no-brainer that technology can bring a lot of value to your products and businesses. However, they can cost quite a lot when unchecked and not used properly, moreover on keeping up with your competitors. To prevent this, identify and select processes that need the support of technology. This can be done by gradually improving the processes that work in your favor.
Conclusion
These are just some of the results of poor practices and management a company can have. You may face these in due time, but to let this not happen; prepare, plan, and enable foresight so that you can act quickly and vigilantly.
One other method to prevent this is to have your operations and shipments be outsourced to a logistics company. They can handle the most complex problems in logistics and save you a buck for additional costs that you may incur.
If you’re having a hard time looking for a logistics service provider, Dash Cargo is here for you. You can trust us with handling your end-to-end logistics requirements such as shipments, documentation, trackers, and even your internal systems. Expect nothing but the best service, solutions, and innovations to make your supply chain and logistics prowess stronger in the global trade industry.